膠木波紋把手的注塑成型工藝詳解
2025-05-30
膠木波紋把手的注塑成型是決定其紋理清晰度、結(jié)構(gòu)強(qiáng)度和表面質(zhì)量的核心環(huán)節(jié),需精準(zhǔn)控制材料塑化、模具溫度、壓力參數(shù)及固化過(guò)程。以下從工藝原理、關(guān)鍵參數(shù)、操作要點(diǎn)及常見問(wèn)題等方面進(jìn)行詳細(xì)解析:
一、注塑成型原理與設(shè)備
1. 工藝原理
熱固性塑料特性:膠木(酚醛塑料)屬于熱固性材料,注塑過(guò)程中需經(jīng)歷塑化熔融→填充模具→交聯(lián)固化三個(gè)階段。
塑化階段:固態(tài)膠木在料筒內(nèi)加熱至熔融態(tài)(線性分子鏈斷裂);
固化階段:在模具高溫下發(fā)生交聯(lián)反應(yīng)(分子鏈形成網(wǎng)狀結(jié)構(gòu)),定型后不可再熔融。
波紋成型關(guān)鍵:模具型腔表面的波紋紋理(通過(guò)雕刻或電火花加工形成)需在填充階段被熔融膠木完全復(fù)制,依賴足夠的壓力和溫度確保熔料充模充分。
2. 主要設(shè)備
注塑機(jī)類型:需使用熱固性塑料專用注塑機(jī)(區(qū)別于熱塑性注塑機(jī)),特點(diǎn)包括:
料筒溫度控制精度高(±2℃),避免膠木提前固化;
具備高剛性鎖模機(jī)構(gòu)(鎖模力≥1000kN),應(yīng)對(duì)高壓注射需求;
螺桿轉(zhuǎn)速較低(10~20r/min),減少剪切生熱導(dǎo)致的材料分解。
輔助設(shè)備:
預(yù)壓機(jī)(用于原料預(yù)壓錠料);
模溫機(jī)(控制模具溫度均勻性,溫差≤5℃);
機(jī)械手(自動(dòng)取件,避免人工接觸高溫模具)。
二、關(guān)鍵工藝參數(shù)與控制
1. 溫度控制
參數(shù) 典型范圍 作用與影響
料筒溫度 140~170℃ - 低溫:塑化不足,熔料含顆粒,導(dǎo)致波紋缺料;
- 高溫:提前固化,堵塞料筒或澆口。
模具溫度 150~180℃ - 低溫:固化速度慢,把手表面發(fā)粘、強(qiáng)度低;
- 高溫:加速交聯(lián),紋理清晰但易過(guò)固化(表面脆化)。
冷卻介質(zhì)溫度 40~60℃ 通過(guò)模具水道循環(huán)水 / 油,控制固化后把手冷卻收縮,避免變形(冷卻時(shí)間占總周期的 30%~50%)。
2. 壓力控制
參數(shù) 典型范圍 作用與影響
注射壓力 50~100MPa - 低壓:熔料無(wú)法充滿波紋細(xì)節(jié),導(dǎo)致紋理模糊;
- 高壓:可能損壞模具或產(chǎn)生飛邊(需配合鎖模力調(diào)整)。
保壓壓力 30~60MPa 維持熔料填充,補(bǔ)償固化階段體積收縮(膠木固化后體積收縮率約 3%~5%),防止把手縮水。
背壓 5~10MPa 螺桿旋轉(zhuǎn)時(shí)的反壓力,用于壓實(shí)原料,減少空氣混入(過(guò)高會(huì)導(dǎo)致原料過(guò)熱分解)。
3. 時(shí)間控制
參數(shù) 典型范圍 作用與影響
注射時(shí)間 5~15 秒 過(guò)短:熔料流速快,易產(chǎn)生湍流和氣泡;
過(guò)長(zhǎng):熔料在料筒內(nèi)停留久,提前固化。
固化時(shí)間 30~90 秒 由把手厚度決定(每 1mm 厚度需 10~20 秒),不足會(huì)導(dǎo)致內(nèi)部未固化(敲擊聲發(fā)悶),過(guò)長(zhǎng)降低效率。
循環(huán)周期 60~150 秒 總時(shí)間 = 注射時(shí)間 + 保壓時(shí)間 + 固化時(shí)間 + 冷卻時(shí)間 + 脫模時(shí)間,優(yōu)化周期可提升產(chǎn)能。
三、操作流程與要點(diǎn)
1. 開機(jī)前準(zhǔn)備
模具安裝與調(diào)試:
檢查模具型腔表面清潔度,使用酒精或壓縮空氣去除油污、粉塵(避免污染波紋紋理);
安裝模具后,手動(dòng)試模確認(rèn)合模對(duì)齊度,調(diào)整鎖模力至模具緊密貼合(無(wú)間隙)。
原料預(yù)處理:
預(yù)壓錠料需在 80℃烘箱中干燥 2 小時(shí)(含水率≤0.5%),避免注塑時(shí)產(chǎn)生氣泡;
顏料與填料混合不均勻時(shí),可增加高速混合時(shí)間至 20 分鐘,確保顏色均勻。
2. 注塑過(guò)程操作
料筒填充與塑化:
采用 “分段式” 料筒溫度控制(進(jìn)料段 140℃→壓縮段 150℃→噴嘴段 160℃),確保原料逐步均勻塑化;
觀察料筒壓力曲線,正常塑化時(shí)壓力波動(dòng)應(yīng)≤10MPa,若驟升需停機(jī)檢查是否有固化塊堵塞。
充模與保壓:
注射速度采用 “慢 - 快 - 慢” 三段控制:
慢速(10mm/s)填充澆口,避免飛濺;
快速(50mm/s)填充型腔主體,確保波紋瞬間充模;
慢速(20mm/s)填充末端,減少湍流。
保壓階段可分兩級(jí):先以 80% 注射壓力維持 10 秒,再降至 50% 壓力維持至固化開始。
3. 脫模與取件
脫模條件:把手表面溫度降至 70℃以下(手感不燙手),固化度≥95%(用硬度計(jì)檢測(cè)表面硬度≥HRR 100);
脫模力控制:頂針行程需與模具設(shè)計(jì)匹配,頂出速度≤30mm/s,避免因應(yīng)力集中拉壞波紋尖端(建議頂針?lè)植荚诎咽址羌y理區(qū)域)。
四、波紋紋理成型的關(guān)鍵技術(shù)
1. 模具紋理加工工藝
電火花加工(EDM):
使用銅電極或石墨電極,在模具鋼表面通過(guò)火花放電腐蝕出波紋紋路,精度可達(dá) ±0.02mm;
紋理深度通常為 1.5~2.5mm,寬度 3~5mm,需根據(jù)把手尺寸調(diào)整(小型把手紋理宜淺,大型把手可加深至 3mm)。
雕刻加工:
五軸 CNC 雕刻機(jī)直接銑削模具型腔,適合規(guī)則波紋(如等距螺旋紋),表面粗糙度 Ra≤1.6μm,需后續(xù)拋光處理以減少熔料流動(dòng)阻力。
2. 熔料充模仿真分析
采用Moldflow 等 CAE 軟件模擬熔料流動(dòng):
分析波紋區(qū)域的填充時(shí)間(應(yīng)≤2 秒),避免熔料前鋒冷卻導(dǎo)致缺料;
優(yōu)化澆口位置,確保波紋各區(qū)域同時(shí)充模(溫差≤5℃),減少熔接痕(如采用對(duì)稱澆口設(shè)計(jì))。
五、常見缺陷與解決方案
1. 波紋紋理缺陷
問(wèn)題 原因分析 解決措施
紋理缺料 注射壓力不足 / 模具溫度低 提高壓力至 80MPa,模溫升至 170℃
紋理模糊 熔料流速慢 / 冷卻速度快 加快注射速度至 60mm/s,降低冷卻水溫至 50℃
飛邊(溢料) 鎖模力不足 / 模具間隙過(guò)大 增大鎖模力至 1200kN,研磨模具分型面
2. 結(jié)構(gòu)性缺陷
問(wèn)題 原因分析 解決措施
內(nèi)部氣泡 原料含水分 / 注射速度過(guò)快 原料干燥處理,降低注射速度至 40mm/s
變形翹曲 冷卻不均 / 固化時(shí)間不足 優(yōu)化模具水道,延長(zhǎng)固化時(shí)間 10~20 秒
嵌件松動(dòng) 嵌件表面光滑 / 熔料溫度低 嵌件表面滾花(粗糙度 Ra≥6.3μm),提高料筒溫度 10℃
六、工藝優(yōu)化與趨勢(shì)
1. 高效生產(chǎn)技術(shù)
多工位旋轉(zhuǎn)模具:在一臺(tái)注塑機(jī)上配置多套模具,實(shí)現(xiàn) “注射 - 固化 - 脫?!?同步作業(yè),產(chǎn)能提升 30% 以上;
模內(nèi)涂層技術(shù):在模具型腔表面噴涂特氟龍涂層(厚度 5~10μm),降低熔料摩擦系數(shù)(μ≤0.1),減少脫模阻力并提升紋理光澤度。
2. 綠色制造工藝
生物基酚醛樹脂:采用植物源苯酚(如從木質(zhì)素提?。┨娲突?,降低碳排放;
廢料循環(huán)利用:將不良品粉碎至粒徑≤0.5mm,按 5% 比例與新料混合(僅限非外觀件生產(chǎn)),減少材料浪費(fèi)。
總結(jié)
膠木波紋把手的注塑成型需以模具精度為基礎(chǔ)、溫度壓力為核心、過(guò)程控制為關(guān)鍵,通過(guò)精細(xì)化參數(shù)調(diào)整和先進(jìn)工藝應(yīng)用,實(shí)現(xiàn)波紋紋理的高保真復(fù)制與產(chǎn)品性能的穩(wěn)定。未來(lái),隨著智能化注塑機(jī)(如配備 AI 參數(shù)自優(yōu)化系統(tǒng))和環(huán)保材料的普及,該工藝將向高效、精準(zhǔn)、綠色方向持續(xù)升級(jí)。
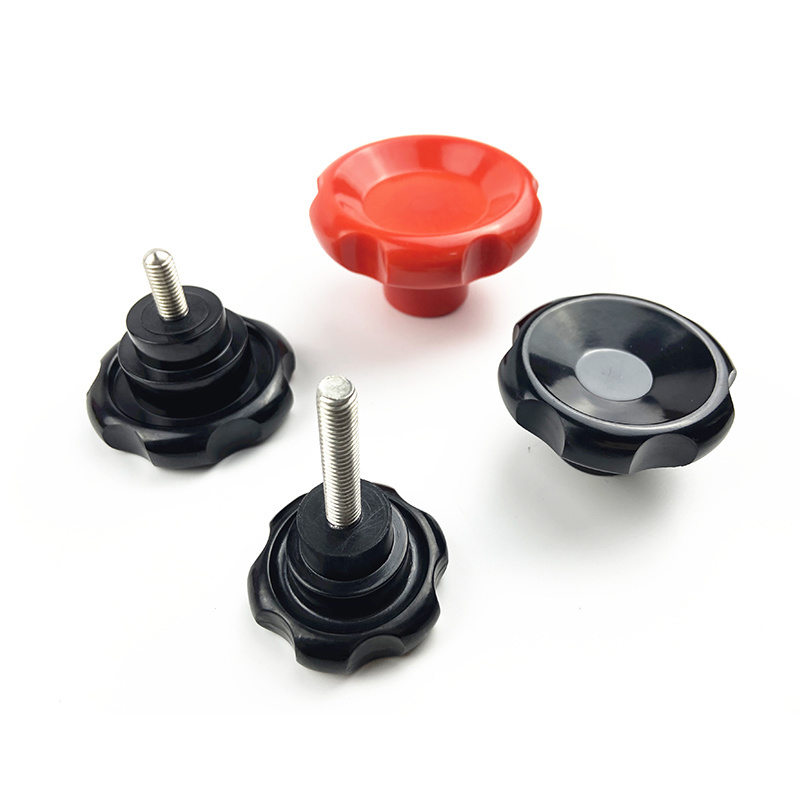
膠木波紋把手的注塑成型工藝詳解
上一條:
下一條:
相關(guān)新聞
相關(guān)產(chǎn)品
聯(lián)系方式
客服熱線:
400-0318-556
市場(chǎng)部聯(lián)系電話(張經(jīng)理) :
19933198222
客服郵箱:
zhangzhe@hbxypj.com
地址:
河北省衡水市深州市南護(hù)工業(yè)區(qū)鑫宇產(chǎn)業(yè)園